碳化鎢立銑刀、鑽頭、鉸刀製造應用
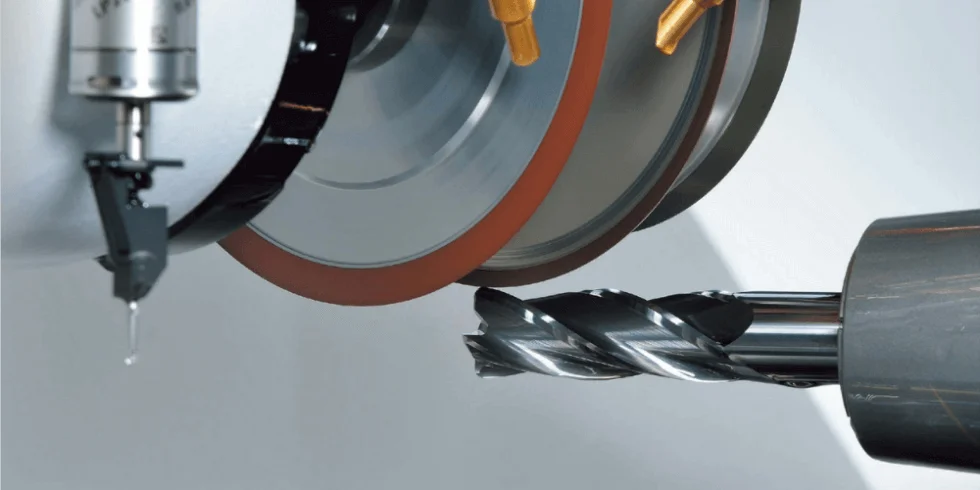
標準立銑刀製造應用
立銑刀,具有一刃或多刀刃的旋轉刀具,是用於銑床上銑削加工的,工作時各刀刃依次間歇地移除工件材料。立銑刀各部位名稱,如圖所示。
刃數
一般立銑刀常見分為2刃或4刃,部份有3刃…等等,切刃數的不同會大大的影響銑刀的性能,例如由如圖1所示2刃比4刃切削槽大,故2刃有良好的排屑能力,但由於截面積較小,刀具本身剛性因此降低,在銑削中易產生彎曲,因此被加工材產生不良銑削面,對加工尺寸精度有較差的表現。4刃的排屑性能較2刃差,由於刀具截面積較大,刀具本身剛性較好,一般使用能得到較好的加工尺寸精度。由於4刃立銑刀的進給為1.5~2倍,故可以得到較好的加工效率。一般的使用為:2刃為通用性加工,例如插銑、槽銑、側銑..等,4刃為中、精加工側銑使用較多。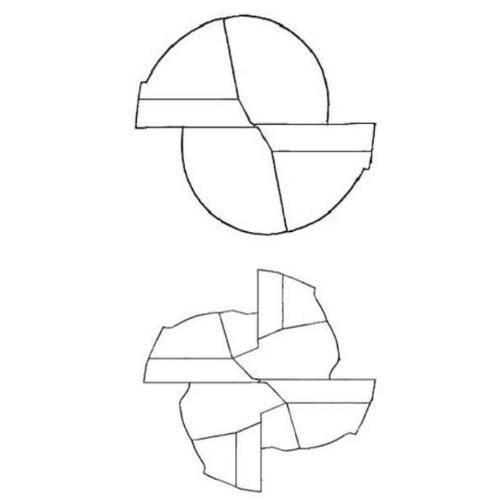
2刃與4刃端面外形比較
螺旋角
右圖所示,螺旋角是為了減少切削中的震動及提高切削銳利度不可或缺的因素。一般使用上螺旋角設計在15゚~ 60゚之間。15゚~ 20゚左右的螺旋角立銑刀用於鍵槽加工。
30~ 35゚左右的螺旋角為一般加工用。
38~ 48゚左右的螺旋角為高效率切削加工用,可使用範圍較為廣泛。
50~ 55゚為高強度螺旋則用於銑削HRC超過50˚的硬化鋼為主。
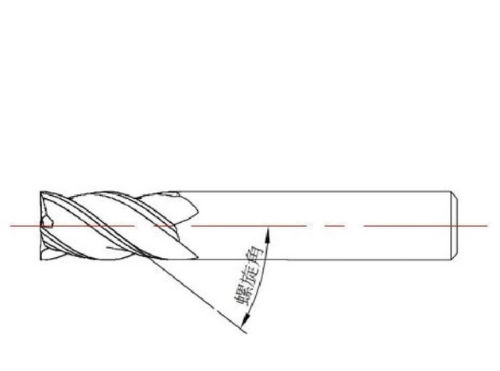
螺旋角示意圖
芯厚
芯厚是決定立銑刀剛性與容屑槽的重要因素。整體上立銑刀的芯厚一般為外徑60%、65%。芯厚增大,截面積增大,剛性提高,但容屑槽減小,排屑性能變差;反之,芯厚減小剛性降低,但排屑性能增強。以下幾種介紹:
標準槽型芯厚
芯厚為刃徑的65%,由平面砂輪研磨排屑槽的型狀,圖示中得知刀刃背部厚度較厚,刀刃強狀較好但排屑較差。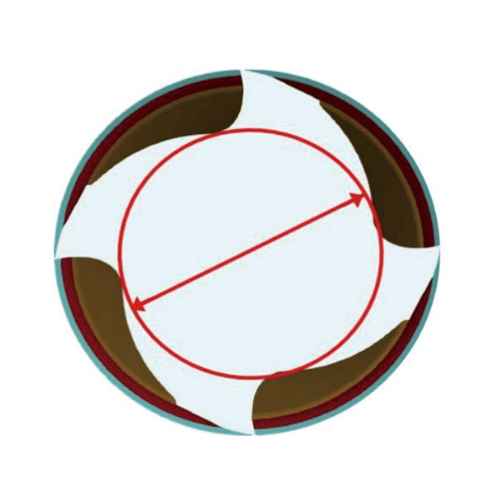
標準槽型芯厚
U 形槽型芯厚
芯厚一樣為刃徑的65%,由成型砂輪研磨U形槽排屑槽的型狀,圖示中得知可以改善排屑效率。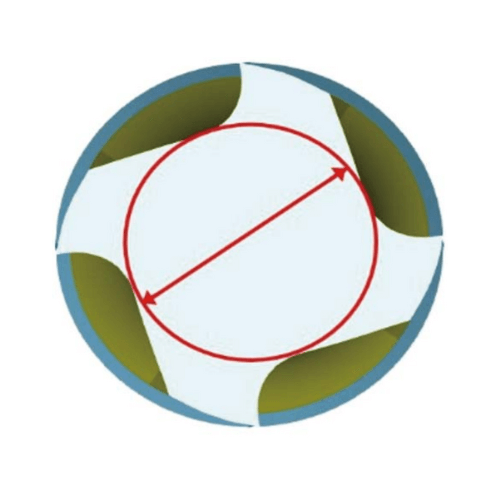
U 形槽型芯厚
不等分割刃槽型芯厚
芯厚為刃徑的50% ~ 60%,由成型砂輪曲線可以研磨出排屑槽具有特殊折痕線可使切屑產生彎曲,使切屑彈出。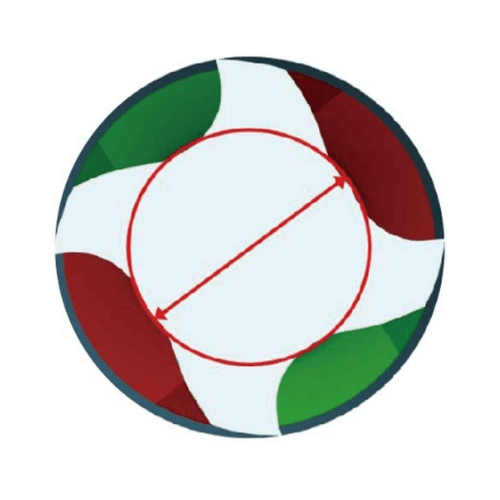
不等分割刃槽型芯厚
高效率鋁用刀槽型芯厚
芯厚為刃徑的45% ~ 55%,由成型砂輪曲線以研磨出大排屑槽,具超高效率切削鋁合金,排屑效果非常好。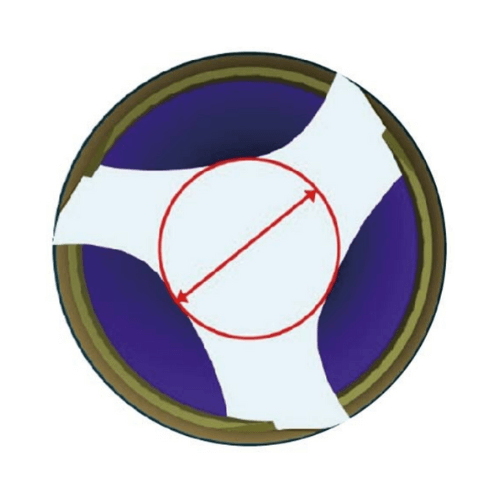
高效率鋁用刀槽型芯厚
切削角γ(前角)
如圖所示,切削角γ的應用,依被切削材條件不同有不同的設計概念。一般非合金鋼材及碳鋼切削設計為γ10゚。
合金鋼切削設計為γ5゚。
硬化鋼HRC50˚~ HRC70˚切削設計為γ-5゚~ γ-10゚。
難切削材中如不銹鋼材為設計γ8˚。
有色金屬中鋁合金為γ15゚~ γ20゚。
.png)
切削角示意圖
外徑離隙角(後角)
依砂輪的選用與研磨方式不同,銑刀的外徑離隙角可分為二種型式:H斜線、N偏心。
H斜線
此型式之離隙角刃口強度較差,刃口非常鋒利,適合軟質材料切削。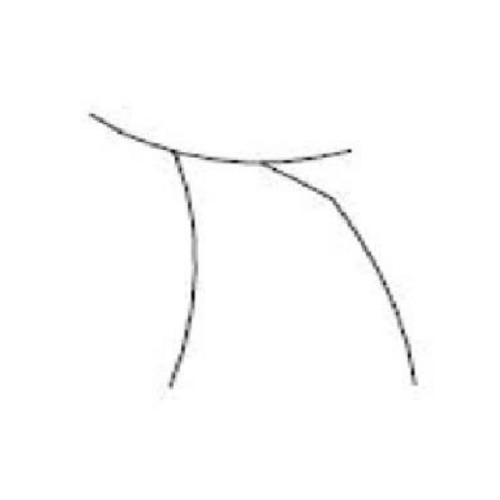
H 斜線示意圖
N偏心
此種具有偏心圓的離隙刃口,根據切削測試顯示,此種刀刃形式,強度與耐磨度為最佳,切削時刃口不易產生崩裂現象,適合鋼鐵材料切削。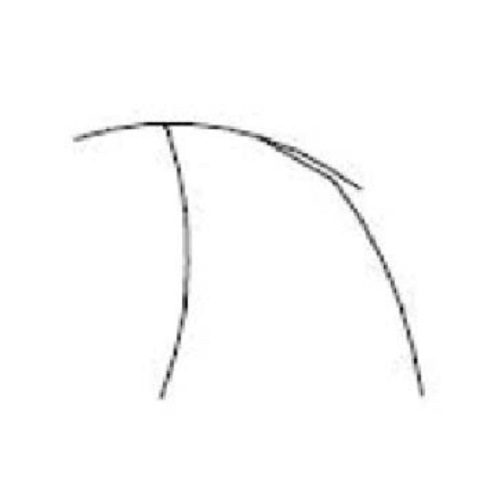
N 偏心示意圖
外徑離隙角(後角)
外徑離隙角磨法搭配分為如下幾種:
H+H
第一離隙角H,第二離隙角H,第一離隙角H角度設計7˚至13˚,第二離隙角H角度設計20˚至25˚,以被切的材料軟硬調整。.png)
H+H 外徑離隙角示意圖
N+H
第一離隙角N,第二離隙角H,第一離隙角N角度設計6˚至11˚,第二離隙角H角度設計25˚至30˚,以被切的材料軟硬調整。.png)
N+H 外徑離隙角示意圖
N+N
第一離隙角N,第二離隙角N,第一離隙角N刃寬可設計為0.03mm~0.1mm,角度設定為0˚至3˚,第二離隙角N角度設計6˚至11˚,以被切的鋼類材料軟硬調整。.png)
N+N 外徑離隙角示意圖
N
第一離隙角N,角度設計6˚至11˚以被切的鋼類材料軟硬調整。.png)
N 外徑離隙角示意圖
外徑刃部外形
外徑刃部外形大致上分為粗加工立銑刀、斜度立銑刀、成型立銑刀。
粗加工立銑刀
又分為波浪齒形粗加工立銑刀、梯齒形粗加工立銑刀:
-
波浪齒形粗加工立銑刀
波浪齒痕可使切屑最小化,降低切削阻力,適合粗銑,由於粗糙操度太大,請不要用於精加工。
.png)
-
梯齒形粗加工立銑刀
梯齒痕可使切屑分屑化,切削阻力比波浪齒痕大,但比標準型立銑刀小,適合粗加工、精加工、對表面粗糙度要求不高的零件可適用。
.png)
分屑槽立銑刀
標準刃外形加上分屑槽,可使切屑分斷並可降低切削阻力,亦可高速切削擺線粗加工、中精加工、精加工。
.png)
斜度立銑刀
用於模具零件拔模斜面的銑削。
.png)
成型立銑刀
用來加工成形表面的專用刀具。其刀具刃部外形輪廓依工件輪廓設計。如
.png)
底刃(刀尖)外形
大致上分為刀尖小C角、R角立銑刀、球頭立銑刀。
刀尖小C角
C角範圍可以落在0.2mm左右,依刃徑大小搭配可增加刀具刀尖壽命。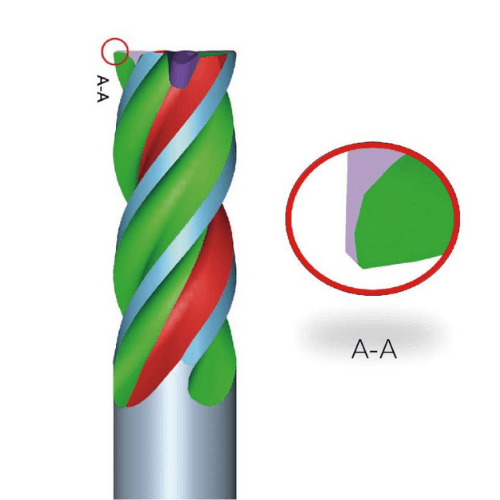
刀尖小C角示意圖
R角立銑刀
一般使用在曲面仿型加工粗加工及精加工,R角部份外型如徑向角和軸向角的搭配會影響加工面。.png)
R角立銑刀示意圖
球頭立銑刀
此形刀具常用於3D曲面精加工,此類形刀具重點在於球頭靜點部位,此部位在加工平面時無切削能力易使平面產生毛刺現象,對此問題提升研磨精細度,使靜點部位更精細,在加工上使曲面與平面光滑度更為一致。
S形球頭外形如圖所示,此設計主要使球頭與工件降低截面積,利於降低切削阻力。
多用途立銑刀製造應用
不等切削設計
3種不等切削設計分為: 不等分割刃、不等螺旋角、不等導程其目的可進行高速加工實現高效率產能,使得加工表面質量穩定可靠,刀具壽命加長,達到為刀具使用者降低成本。
不等分割刃
利用徑向刃口切入時間點不同,會有不同的頻率的產生來達到抑震。
不等螺旋角
利用螺旋角不同,使刀具軸向刀刃切入工件的時間間隔不同,即產生一組不固定的頻率,來干擾既有的頻率穫得減少或消除震動,螺旋角角度差可落在2˚或3˚,刃長越長影響排屑槽大小要納入考量。.png)
A=A≠B=B 不等螺旋示意圖
不等導程
利用每一刃的螺旋角,角度在不同區間變化,使刀具切削中產生更多微小頻率,進行干擾使得產生共振的機率越小。刀具穫得消除震動效果,刀具使用自然可以大進給及高速切削,此時建議使用強力刀桿夾持。.png)
不等導程示意圖
範例設計
近幾年CAM的軟體功能越來越強大,延伸出高速切削擺線加工法。因應此工法設計刀具:
- 鎢鋼材質挑選。
- 從刃數上考量可設5刃、6刃 或 7刃,來提高切削進給速度。
- 從螺旋角越大排屑槽就會密會影響到排屑槽大小,螺旋角越小且切削力就會越大,因此會建議把螺旋角設計38˚至48˚範圍。
- 因是高速切削的刀具,不等分割刃、不等螺旋角設計概念就可以加入來降低震動。
- 因工法會是軸向切削深度深,切削寬度小,刀具刀刃上可以加入分屑槽設計及芯厚可設計為刃徑70% ~ 75%,加強鋼性來降低刀具的饒曲。
- 端面部份刀尖可以設計C角或R角來增加刀尖壽命。
- 切削被材料來決定切削角和離隙角。
- 塗層配方挑選。
.png)
分屑槽示意圖
碳化鎢鑽頭製造應用
鑽頭各部位名稱介紹
鑽頭是一種旋轉且沿主軸進給的切削刀具,利用頂端的切刃移除工件材料,在工件上產生孔的刀具。鑽頭各部位名稱,如圖所示。
螺旋角
螺旋角是形成鑽削切入不可或缺因素之一,具有增加鑽頭銳利及排屑等作用,以下分析介紹螺旋角角度大小利害關係。
螺 旋 角 |
大 ↓ 小 |
低 | 低 | 小 | 差 |
鑽頭 剛性 |
切刃 強度 |
切削 阻力 |
切屑 排出 |
||
高 | 高 | 大 | 好 |
切刃強度、切削阻力
螺旋角 = 切刃外周的前角及切刃強度。一般來說,螺旋角越大,主切刃的前角就越大,及剛性就越差。下圖所示。
切屑排出
螺旋角越大切屑排出的距離就越長,因此,切屑在孔內壁及鑽頭槽的干涉,切屑排出速度變慢,容易發生切屑阻塞。
以上螺旋角概念介紹,我們一般設計螺旋角會落在15゚~40゚之間,一般鋼材、鑄鐵、不鏽鋼,螺旋角為20゚~ 30゚,
有色金屬,螺旋角則30゚~ 40゚,塑膠、黃銅,螺旋角則15゚~ 20゚,以上舉例幾項可以作為設計參考或者挑選鑽頭。
鑽頂角
鑽頂兩切削邊所夾角角度稱為鑽頂角。以下分析介紹鑽頂角角度大小利害關係。
切削性能、切削阻力
如圖所示,得知鑽頂角角度越大阻力就越大,鑽頂角角度越小阻力小。
鑽 頂 角 |
大 ↓ 小 |
劣 | 優 | 大 | 小 |
切削 性能 |
切屑 處理 |
切削 阻力 |
出口 毛刺 |
||
優 | 劣 | 小 | 大 |
切屑處理
如下圖所示,可依公式 F x COS﹝﹙180 – 鑽頂角﹚/ 2﹞得知鑽頂角角度越大切屑處理能力就越優,鑽頂角角度越小切屑處理能力劣。
出口部位毛刺
鑽頂角越大與外周圓夾角就越小,相對的就峰利,出口少毛刺就越少。鑽頂角越小與外周圓夾角就越大,相對的就不峰利,出口少毛刺就越多。如下圖所示
然而各切刃與中心線所夾角角度應相同,若兩夾角不同則鑽削時易引起鑽頭晃動,而導致使切刃易崩角現象,甚至使孔徑擴大。以上鑽頂角概念介紹。以下舉例幾項常見依材料特性可以作為設計鑽頂角作為參考。一般鑽軟材鑽頂角會採118゚,合金鋼會採140゚。不銹鋼為135゚。
鑽唇離隙角
鑽唇離隙角,鑽頭切刃與刀腹面形成之角度,避免回彈造成刀刃被彈破、減少和工件的摩擦,與被加工材料的楊氏係數與韌性有關。以下舉例幾項可以作為參考。一般鋼材鑽唇離隙角設計為10゚~13゚、硬化鋼鑽唇離隙角為6゚~ 9゚,不銹鋼鑽唇離隙角為8゚~ 12゚。
鑿刃&鑿刃削薄
如圖所示,兩刃腹面在鑽頭頂短端的交線稱為鑿刃又稱為靜點,其幾何形狀為正交於鑽軸且趨近於直線形狀,正因如此,在鑽頂接觸工作平面時,發生鑽尖自走現象。
鑿刃的中心必需與鑽頭軸線同心,於鑽孔時有穩定作用,若不在同一中心,則鑽頭會產生晃動、易折斷,且所鑽孔之尺寸會擴大。
如圖所示,非削薄鑽頭和X形削薄鑽頭的推力負載的比較。非削薄鑽頭的鑿刃會產生很大的推力負載,此負載會隨鑿刃長度而增加。當有削薄設計時,鑿刃長度會縮短,推力負載幾乎消除了。因此鑿刃削薄非常重要,因為它解決了振動引起的崩刃和毛刺等問題,提高孔精度。
主切刃&K-Land
為鑽槽和鑽腹於鑽頂的交線,稱為主切刃。此部份注意的地方兩切削邊與鑽頭中心軸所夾之夾角應相同,且切邊長度應相等,否則將造成單邊切削,鑽刃易鈍化而崩裂,孔徑擴大和鑽削擺動等問題。
主切刃設計有K-Land寬設計可增加40%~60%壽命,以下舉例幾項可以作為參考。
材料 | 鋁合金 | 鑄鐵 | 一般鋼 | 合金鋼 | 不銹鋼 |
---|---|---|---|---|---|
K-Land寬 | 0~0.02 | 0.02~0.05 | 0.08~0.12 | 0.10~0.15 | 0.03~0.08 |
刃帶
- 刃帶作用:保持鑽頭的尺寸。支稱孔壁,自導向,能在加工中起穩定鑽削的作用。
- 雙刃帶作用:孔尺寸精度和形狀精度(真圓度)的提高。孔的表面質量提高。深孔加工較穩定。
- 刃帶寬度考量因素:孔的直度、孔的精度,刃帶寬度應加寬。材料加工硬化,如不銹鋼材料加工中切削產生熱引起孔內面硬化,刃帶寬度應縮窄。
倒錐
倒錐作用,為了減少鑽頭鑽削時外圓刃帶與孔璧的摩擦,其倒錐度一般取每100 mm長度上為0.03 ~ 0.1 mm。對於高速鑽頭及鑽削彈性變形較大或黏性材料,倒錐值可以設定0.2 ~ 0.4 mm。
碳化鎢鉸刀製造應用
鉸刀具有多個齒刃,一般為偶數刃居多,用於切除已加工孔,表面薄層金屬的旋轉刀具。具有直刃或螺旋刃的刀具,用於擴孔或修孔,經過鉸刀加工后的孔可以獲得孔的加工尺寸精度及降低其表面粗糙度。鉸刀各部位名稱,如圖所示。
刃數&等份&不等份
鉸刀的齒數根據其刃徑大小、加工精度和刃槽容屑空間大小而決定。一般取偶數,便于量測其刃徑,鉸刀齒距在圓周上可做成等份的也可以做不等份的。後者的目的在於,避免鉸孔時在孔壁上周期性產生痕跡。
螺旋角
鉸刀的螺旋角一般上做成直刃形(0˚)。對於鉸削非連續表面的孔或為了進一步要求被鉸孔的表面粗糙度,可設計成螺旋刃形,其有分為左螺旋和右螺旋這會影響排屑的方向。
.png)
.png)
.png)
切削角γ(前角)
於鉸削的預留量較小,切削僅在刀尖進行,與刀齒的前傾面很少觸,一般設為0度。亦可針對性被鉸削材料不同,以下舉例幾項可以作為參考。
鑄鐵: γ= 0˚硬鋼:γ= 0˚~ 3 ˚
軟鋼、銅、鋁合金:γ= 6˚~ 8 ˚
合金鋼、不銹鋼:γ= 8˚~ 10 ˚
耐熱鋼、高鉻不銹鋼:γ= 8˚~ 10 ˚
硬化鋼:γ= -15˚~ -5 ˚
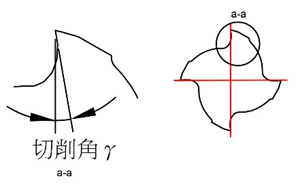
切削角γ示意圖
刃帶&倒錐
刃帶
鉸刀校正部份外徑及其倒錐外圓表面上均需留有刃帶,這是為了便於量測鉸刀刃徑並在鉸削過程中保持穩定。其外圓刃帶表面粗糙度參數值應低於被加工孔表面粗糙度1~2級。其刃帶寬度設刃徑的0.02~0.03倍率,寬度大小會影響到鉸孔的尺寸精度(擴孔及縮孔)及表面粗糙度
倒錐
倒錐部份為避免外圓刃帶表面與鉸削後表面的磨擦不致刮傷表面。倒錐度的數值一般設定為0.03~0.04/100 mm (每100mm ,大徑與小徑差值),亦可針對性被鉸削材料不同,以下舉例幾項可以作為參考。鉸削青銅、黃銅、鑄鐵、鋁合金及其它輕合金時,為 0.03~0.05/100 mm。鉸削軟鋼、中硬鋼時,為 0.05~0.07/100 mm。鉸削合金鋼、不銹鋼時,為 0.07~0.10/100 mm。鉸削耐熱鋼、高鉻不銹鋼時,為 0.1~0.25/100 mm。
導引錐
為便於導入孔中,在鉸刀前端一般研磨出 45˚ 導入角,高合金鋼和硬化鋼可設計 25˚ ~ 30˚ 導入角。