- Home
- TECH & KNOWLEDGE
- Cutting Tools Knowledge
- Cutting Tools | Milling Cutter | 4 points to guide you to choose the right End Mills!
Cutting Tools | Milling Cutter | 4 points to guide you to choose the right End Mills!
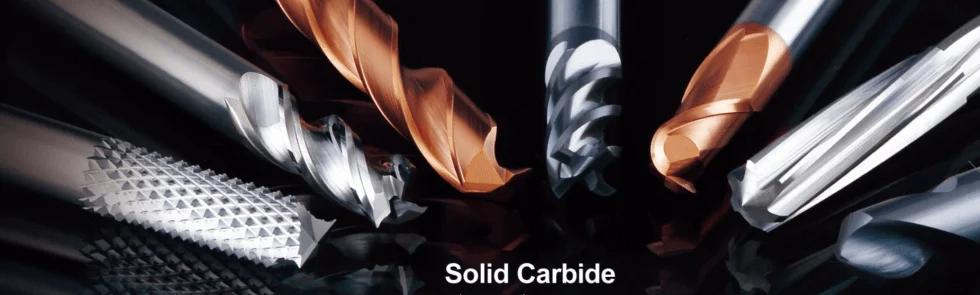
Cutting tools are important tools for metal processing. Cars need engines, TVs need circuit boards, air conditioners need motors...these delicate parts are made by metal processing. Metal processing techniques need to be achieved by cutting tools, and what types of cutting tools are available? What are the uses? How to choose the end mills? This article will bring you a preliminary understanding of cutting tools, read on!
Cutting tool applications
Cutting tool is a tool made for cutting processing, then what is cutting processing? Simply put, cutting tools are installed on the processing machine to cut and carve the metal blocks. In fact, the processing methods include: milling, drilling, planing, grinding, turning..., the appearance and material of the cutting tools used in different processing methods are also very different. As the old saying goes, "To be good at what you do, you must first be good at what you do". You need strong cutting tools to produce accurate metal products, and poor-quality tools may have the risk of broken tools flying out during the cutting process, which increases the cost. To choose to use a strong and durable milling cutter to create a smooth and smooth appearance of the finished product, accurate control of the size to increase the yield of the finished product.
Types of cutting tools
The above mentioned metal processing methods are: milling, drilling, planing, grinding, turning, etc. The cutting tools required for different processing methods are of course different, and the four common cutting tools are introduced here.
Drill Bit
Drill is the most common hand tool in daily life, usually used in our woodworking DIY or wall hanging needs. It mainly relies on the bottom of the tool for drilling operations, and is a cutting tool with a spiral appearance, which on the one hand can carry the chips away from the drilling place, and on the other hand can inject cutting fluid along the spiral track to protect the drill bit. Not only in the household sector, but also in the industrial parts, electronic panels and manufacturing industries, there is a large demand for drills, and many different styles and materials of drills have been developed for different drilling conditions. For example, the drill bit for enlarging the hole, the center drill bit for precise positioning for subsequent deep drilling, or the deep hole drill bit for drilling hard metals.
End Mill | Milling cutter
Milling cutter, also known as end mills or flat mills, are similar in appearance to drills, but they are very different in function. The drill mainly relies on the front end to penetrate and the tool must be placed in the same direction as the cutting direction; while the front end of the end mill can also cut, it mainly relies on the side cutters. Therefore, the placement of the end mill is mostly perpendicular to the cutting direction or at a specific angle during cutting, and rarely in the same direction. The main task of end milling cutter is to cut grooves, stepped or streamlined surfaces in the cutting object, which is a common machining requirement in metal processing and is therefore often used in industry.
Reamer
The first is to enlarge the size of the hole, which is the same as the function of the reaming drill. The second and most important function is to smooth the inner wall of the hole, which is a cutting tool for fine machining, therefore the number of edges of reamers in the market is mainly 4, 6 and 8 flutes.
Thread Milling Tools | Thread Mills
As the name implies, a thread milling cutter is a cutting tool for producing internal threads. Also called screws tapping. This method of production requires the size of the taps to be matched in order to produce the corresponding size of internal threads, which not only takes more time, but also has limited accuracy. However, with the advent of computer-controlled processing machines, thread milling cutters can be computerized to produce precise thread, and one thread milling cutter can produce holes bigger than itself, eliminating the need to use a specific size of thread milling cutter for the size of the hole and speeding up the production process significantly.
How to choose the cutting tool, 4 key points to share!
There are so many different cutting tools, how to choose one? Because there are many details of cutting tools, we have compiled four points of selection below to further analyze the purpose of end mill type, cutting edge number, cutting body length, and tool material, so that you can have more direction when selecting a cutting tool.
Types of End Mills
Different types of end mills are processed for different purposes and objects, and the type of end mill refers to the fact that the same type of cutting tool can process different products because it has different cutting heads. The common types of cutter heads are: flat end mills (square end mill), corner radius end mills, ball nose end mills, chamfering mills, Routers, etc. For example, the pointed drill, which can simply drill a groove in the bit, and the flat drill, which can drill a flat hole, the former has stronger penetrating power, while the latter can place the relevant parts inside the hole, all according to the user's needs.
Cutting Flutes
The number of cutting flutes determines how much a cutting tool can cut at one time, and is related to chip evacuation, cutting strength and cutting precision. Tools with fewer edges can cut a larger area and accommodate more chips, and the edge area can also withstand greater resistance, so they often play a pioneering role and are used as the first cut when a large amount of cutting and removal is required. The large amount of chips to be removed at one time also means that fine dressing is not possible, so a tool with more cutting edges comes in handy to limit chip evacuation and cutting intensity to improve the accuracy of cutting and is very suitable for dressing after the second cut. In the case of end mills, they can be used for grooving, roughing or finishing depending on the number of cutting edges selected.
Length of Shank
The length of the shank may be ignored by some people, but in fact is related to the size and depth of the object to be cut. If the object to be cut is deeper, a shank that is not long enough will not be able to cut, so you need to pay attention to it when you buy it. However, not the longer the shank is the better, you need to adjust the cutting angle, speed, and rotation speed according to the end mill quality to avoid chipping or broken blade.
Tool Material
The material of the cutting tool determines what kind of object it can cut. Common tool materials include: the high-carbon tool steel, which is often used for slow cutting tools such as reamers; the hard and tough high-speed steel, which is used for drills and can withstand machining steps at higher cutting speeds; the extremely hard, but also more expensive solid carbide for end mills, can be used to cut hard materials. In terms of cost and productivity, there is no best material, only the most appropriate one.
Conclusion
I believe that seeing here you have a certain concept of how to choose cutting tools, without cutting tools, our life can not appear in these diverse and convenient metal products, and good cutting tools can make the product size more accurate, speed up the production speed and reduce production costs. 7leaders has been cooperating with Swiss manufacturers for years. We use extremely hard and tough tungsten carbide, combined with our exclusive production technology, and our tools have been tested many times and are recognized by the industry as an advantageous tool manufacturer with higher wear resistance and longer tool life. In addition, we have 150 sets of tool production equipment space and professional quality control inspection team, 100% online inspection during production to ensure the accuracy of the products, to meet your needs for all cutting tools, welcome to contact us at any time.
- Recent Articles
- Selecting a Milling Cutter Manufacturer: Key Considerations
- Understanding Tungsten Steel and Top-Quality Cutting Tool Recommendations!
- What is a milling cutter? What are the types and specifications?
- What is a drill bit? What are the different types?
- What is a Thread Mill? How to Choose? Get to Know in 3 Minutes!
- Hot Articles
- Understanding Tungsten Steel and Top-Quality Cutting Tool Recommendations!
- What is a drill bit? What are the different types?
- What is a milling cutter? What are the types and specifications?
- What types of milling cutter are there? 3 directions for choosing a quality milling cutter.
- Cutting Tools | Milling Cutter | 4 points to guide you to choose the right End Mills!