- Home
- TECH & KNOWLEDGE
- Cutting Tools Knowledge
- Understanding Tungsten Steel and Top-Quality Cutting Tool Recommendations!
Understanding Tungsten Steel and Top-Quality Cutting Tool Recommendations!
August 14,2023
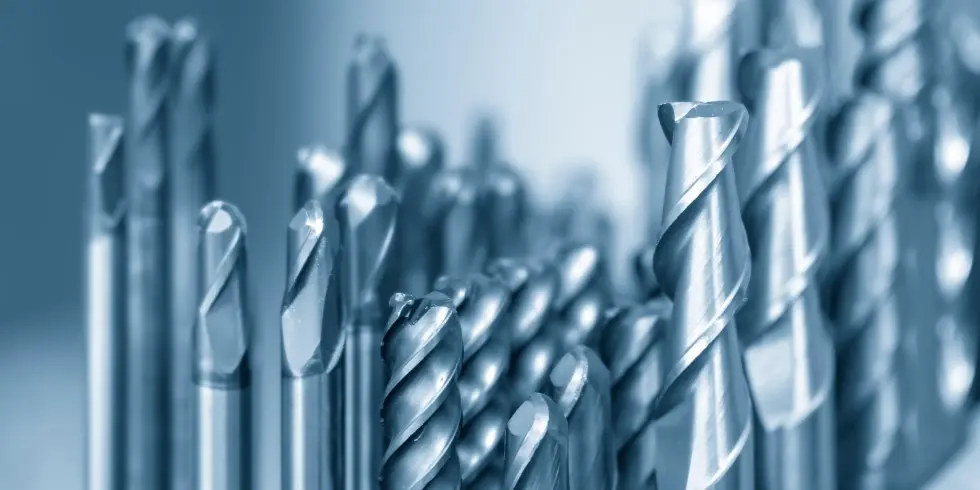
Tungsten carbide steel, renowned for its exceptional qualities such as high hardness and wear resistance, contributes to enhanced stability and prolonged sharpness of cutting tools during the machining process. This, in turn, extends the lifespan of the tools. Currently, it finds widespread application in the field of cutting tool manufacturing. In this article, we will introduce you to the material and characteristics of tungsten steel, concluding with recommendations for excellent high-quality tungsten carbide steel cutting tool products. Whether you are a professional engineer or a manufacturer, the content below is a must-read. We believe these recommendations will offer you practical and valuable insights!
〈Further Reading: Cutting Tools | Milling Cutter | 4 points to guide you to choose the right End Mills!〉
What is Tungsten Steel?
Tungsten carbide steel is a hard alloy composed primarily of tungsten carbide and cobalt. It also contains small amounts of other tungsten carbide steel types, such as titanium carbide, niobium carbide, and tantalum carbide. The manufacturing process involves grinding the constituent raw materials into powder and then sintering them. Tungsten steel possesses attributes like high hardness, exceptional wear resistance, high toughness, corrosion resistance, high-temperature resistance, and stability. It finds extensive applications not only in cutting tools and high-temperature equipment manufacturing but also in jewelry, molds, as well as precision components like bearings and shafts. Tungsten carbide steel material is an ideal choice for the manufacturing industry.Tungsten Steel Milling Tool Characteristics
Tungsten carbide steel milling tools are primarily used in milling operations. They are rotating tools composed of multiple cutting edges, capable of removing a predetermined amount of material on lathes and milling machines. Leveraging the exceptional performance of tungsten carbide steel, they find wide-ranging applications in various tool manufacturing fields, such as mold processing, CNC engraving, and industrial component fabrication. These tools are known for their efficiency and durability. They can handle materials of varying hardness and intricate workpieces with remarkable efficiency, particularly those with hardness below HRC48. This capability provides excellent cutting performance, second only to diamond in hardness, with exceptional wear resistance. Tungsten steel tools maintain their sharpness during the cutting process and exhibit stable cutting performance even under high-temperature and high-pressure conditions. They effectively resist tool wear, extend tool lifespan, enhance machining quality and efficiency, making them suitable for high-speed cutting applications. They contribute to the production of parts and tools required in fields like aviation, automotive, and industry. Moreover, modern tungsten steel milling tools often incorporate nanocomposite multilayer coatings, further enhancing wear resistance and precision, while reducing wear and tear.〈Further Reading: What is a milling cutter? What are the types and specifications?〉
Recommended Tungsten Steel Cutting Tools
1. E140HX Multipurpose End Mills
The E140HX Multipurpose End Mills is a 4-flute high-performance coarse milling cutter. It is suitable for rough machining of steel and iron materials, as well as cutting processes for carbon steel, alloyed steel, stainless steel, cast iron, aluminum, copper, titanium alloys, nickel, and high-temperature alloys. The face mill itself employs MG ultra-fine tungsten carbide steel material, enhancing wear resistance and enabling it to withstand high-pressure cutting. The unequal division design of the cutting edges effectively reduces cutting resistance, thereby boosting machining efficiency. Moreover, the small corner radius design at the cutting edge, combined with the AlCrN nanocomposite multilayer coating, further extends the tool's lifespan, ensuring a more sustained and stable cutting performance. The outstanding characteristics of the E140HX Multipurpose End Mills mill make it an ideal choice for rough machining of steel and iron materials, providing reliable cutting solutions and a superior machining experience for industrial processes.Learn more>>E140HX Multipurpose End Mills
2. B222X Ball Nose End Mills
The B222X Ball Nose End Mills are 2-flute round head face mills designed for cutting processes in various materials, including steel, carbon steel, alloyed steel, hardened steel, stainless steel, cast iron, and copper. What sets this face mill apart is its utilization of a nanocomposite multilayer coating, providing exceptional wear resistance to the tool. The unique S-type ball head geometry ensures that the tungsten steel milling tool maintains a stable cutting performance over prolonged usage, effectively reducing vibrations and friction, leading to more precise and efficient cutting. For materials with hardness below HRC48, this face mill can achieve effective machining results. Whether in precision machining, manufacturing industries, or diverse cutting applications, the B222X Ball Nose End Mills demonstrates outstanding performance, making it a trusted choice for a wide range of machining professionals!Learn more>>B222X Ball Nose End Mills
7Leaders High-Quality Solid Carbide Tooling
7Leaders specializes in producing high-quality solid carbide cutting tools, including thread mills, face mills, drills, and reamers. With state-of-the-art equipment from Germany and Switzerland, they have established a seamless 24-hour production line. The research and development team continually optimizes the technology of solid carbide tooling, conducting cutting tests using cutting-edge carbide materials from around the world to enhance machining performance. They also incorporate the latest Swiss coating technology to create tools with high durability and precision, making them an excellent choice in terms of cost-effectiveness. The product range covers face mills, drills, reamers, thread mills, and more, marketed globally under their own brand. They have maintained strict control over product quality over the years, aiming for high cutting performance, precision tools, and stability in usage. The provided tooling products exhibit a 30% reduction in wear rate compared to other brands, showcasing exceptional wear resistance and superior edge smoothness. This demonstrates outstanding reliability, enabling the rapid removal of materials within a short period while ensuring consistent machining. These tools find extensive application in various fields such as mechanical parts, molds, aerospace, electronics, watches, sports equipment, and medical industries.〈Further Reading: What is a drill bit? What are the different types?〉
Conclusion
From the text, it is evident that high-quality solid carbide cutting tools play a pivotal role. The exceptional performance and durability of solid carbide tools not only lead to higher machining efficiency but also enhance the quality of processed workpieces and extend tool lifespan. As cutting machining techniques continually advance, the performance of carbide tools must constantly improve to ensure more efficient and precise processing. This, in turn, increases productivity and product quality. 7Leaders' manufacturing of solid carbide cutting tools not only involves carefully selected carbide materials but also utilizes the latest Swiss coating technology. This makes them the optimal choice for high-value cost-effectiveness. If you wish to acquire more detailed information, please feel free to contact us.- Recent Articles
- Selecting a Milling Cutter Manufacturer: Key Considerations
- Understanding Tungsten Steel and Top-Quality Cutting Tool Recommendations!
- What is a milling cutter? What are the types and specifications?
- What is a drill bit? What are the different types?
- What is a Thread Mill? How to Choose? Get to Know in 3 Minutes!
- Hot Articles
- Understanding Tungsten Steel and Top-Quality Cutting Tool Recommendations!
- What is a drill bit? What are the different types?
- What is a milling cutter? What are the types and specifications?
- What types of milling cutter are there? 3 directions for choosing a quality milling cutter.
- Cutting Tools | Milling Cutter | 4 points to guide you to choose the right End Mills!
- Article keywords
- 碳化鎢鋼
- tungsten carbide
- 炭化タングステン