- Home
- TECH & KNOWLEDGE
- Cutting Tools Knowledge
- What is a milling cutter? What are the types and specifications?
What is a milling cutter? What are the types and specifications?
June 14,2023
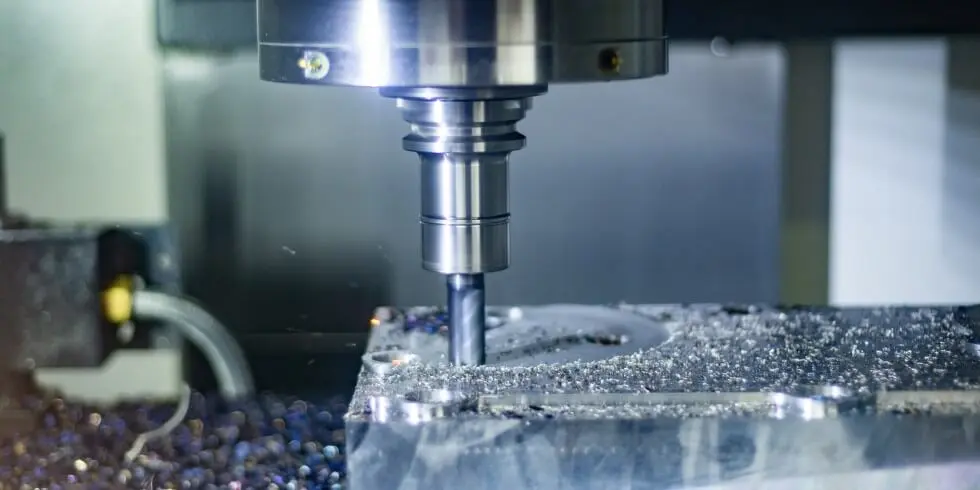
When we are performing milling operations on a milling machine or machining center, we require one or more rotating tools with cutting edges to intermittently remove material from the workpiece, resulting in a smoother and more refined surface. These tools are known as milling cutters. In this article, we will explore the characteristics, principles, types, and selection criteria to provide you with a clearer understanding of milling cutters.
<Product Guide:Multi-Purpose End Mills>
<Product Guide:End Mills for Aluminum>
<Product Guide:Chamfer End Mills>
What is a milling cutter? 3 aspects to help you understand better!
A milling cutter is a spiral tool formed by chip flutes and cutting edges. It is available in various configurations such as 2-flute, 3-flute, 4-flute, etc. It primarily functions by removing material through a fixed feed rate within the machine. Now, let's provide you with a detailed introduction to the characteristics, operating principles, and application range of milling cutters:Characteristics of Milling Cutters
As mentioned earlier, milling cutters are cutting tools formed by combining chip flutes and spiral-shaped cutting edges. Therefore, during the cutting process, each cutting edge sequentially removes material from the workpiece. The cutting personnel adjust the workpiece displacement based on the feed rate per edge (fz in mm/edge) to achieve the cutting effect.Operating Principle
The operating principle of milling cutters is not complicated. They are fixed on a plane and rotate, while the workpiece to be cut is fed into them. Each tooth of the cutter removes a small amount of material. Milling cutters can be categorized into climb milling and conventional milling based on the cutting direction:Climb Milling
Climb milling, also known as up milling, refers to the milling direction being the same as the feed direction. The primary cutting action occurs on the unprocessed surface of the workpiece, and the chips go from thick to thin. Due to less friction during the machining process, the milling cutter's cutting edge has a longer lifespan. Additionally, because of the ease of clamping without vibration and the high precision of the machined surface, it is suitable for milling long and slender workpieces. However, it is important to note that climb milling is not suitable for milling castings, forgings, or workpieces with scales on the surface.Conventional Milling
In conventional milling, the milling direction is opposite to the feed direction, resulting in an upward cutting direction. Therefore, the chips go from thin to thick. Although it can be used on older milling machines, it has some disadvantages such as increased friction, faster dulling of the cutting edge, shorter tool life, increased vibration, rougher surface finish, and lower machining accuracy. As a result, except for the initial milling of castings or the use of older milling machines without backlash removal devices, most applications prefer climb milling, which provides better milling results.Application Range
Milling cutters have a wide range of applications, from simple cutting of workpieces and machining of grooves to precision part manufacturing. They can be used in various industries, including mechanical components, precision molds, automotive parts, aerospace, electronic communications, watchmaking, eyewear, sports equipment, and the medical industry. These are all areas where milling cutters find application.Types of Milling Cutters? Understand the Types and Uses at Once!
There are numerous types of milling cutters, with the basic types being face milling cutters and end mills. However, currently, the majority of options available in the market are end mills. Based on their applications, they can be further categorized into multi-purpose end mills, end mills for aluminum, and chamfer end mills. Let's take a detailed look at each type:End Mills
End mills are commonly used cutting tools in metal machining. Depending on the cutting purpose and material, there are various specific types of end mills available. In terms of applications, they can be broadly classified into the following three categories:Multi-Purpose End Mills
Our multi-purpose end mills are primarily available in 4-flute designs, with special tool geometries for different applications. They can be used for roughing, medium, and finishing operations. The multi-purpose end mills with different coating materials can be selected based on the hardness of the metal to be cut.<Product Guide:Multi-Purpose End Mills>
End Mills for Aluminum
End mills for aluminum are designed with 2 to 3 flutes, providing more chip clearance space. They feature sharp cutting edges and high precision grinding, resulting in finer surface finishes. They are suitable for both roughing and finishing operations and can be applied to various aluminum alloys and copper.<Product Guide:End Mills for Aluminum>
Chamfer End Mills
Chamfer end mills come in various shapes, including pointed tip resembling a drill bit and flat-headed designs. They are available in 2 to 4-flute configurations, mainly categorized by the chamfer angle. For example, our chamfer end mills come in different angles such as 30°, 60°, 90°, and 120°. Depending on the specific model and angle, they can be used for front chamfering, back chamfering, V-groove milling, and more. If you're unsure about the best choice for your needs, feel free to contact our specialists for personalized recommendations.<Product Guide:Chamfer End Mills>
Types | Multi-Purpose End Mills | End Mills for Aluminum | Chamfer End Mills |
---|---|---|---|
Appearance Features | Mostly 4-flute design with different hardness coatings | 2-3 flute design with sharp cutting edges | Available in pointed or flat-end shapes, with 2-4 flute designs |
Applications | Suitable for rough, medium, and fine machining | Ideal for rough and fine cutting operations in aluminum alloys and copper | Used for front chamfering, back chamfering, V-groove machining, spot drilling, and contour milling operations |
How to Choose the Right Milling Cutter? 2 Purchasing Directions to Guide You
When purchasing a milling cutter, how do you select the appropriate product? Typically, we analyze suitable milling cutter options based on the material to be cut and the hardness of the workpiece. In the following, we will explain based on the two aspects mentioned above:Cutting Material
Different materials require suitable cutting tools. For example, aluminum alloys, stainless steel, and ferrous materials are better suited for end mills. On the other hand, composite materials with a high fiber content are recommended to be machined using staggered tooth slotting cutters to effectively cut through the fibers.Workpiece Hardness
Understanding the hardness of the workpiece enables us to recommend suitable milling cutters. For example, aluminum alloys are the softest and lightest metal materials, making them suitable for uncoated and sharper milling cutters. On the other hand, for harder workpieces, we can select tools with different coating materials based on their hardness and material properties. Coatings can increase hardness and provide lubrication, making them suitable for workpieces that are prone to chip adhesion.Conclusion
To procure the right milling cutters, it is essential to assess their intended usage and consider factors such as strength and chip evacuation when selecting the number of flutes. Additionally, we recommend consulting with professional advisors to truly find the appropriate production equipment for your company, reducing costs and maximizing profits. With over 30 years of experience, we offer a wide range of high-performance, high-precision, and highly stable tungsten carbide cutting tools, creating maximum planning benefits for all our partners. If you have any needs for purchasing milling cutters, please feel free to contact us.- Recent Articles
- Selecting a Milling Cutter Manufacturer: Key Considerations
- Understanding Tungsten Steel and Top-Quality Cutting Tool Recommendations!
- What is a milling cutter? What are the types and specifications?
- What is a drill bit? What are the different types?
- What is a Thread Mill? How to Choose? Get to Know in 3 Minutes!
- Hot Articles
- Understanding Tungsten Steel and Top-Quality Cutting Tool Recommendations!
- What is a drill bit? What are the different types?
- What is a milling cutter? What are the types and specifications?
- What types of milling cutter are there? 3 directions for choosing a quality milling cutter.
- Cutting Tools | Milling Cutter | 4 points to guide you to choose the right End Mills!
- Article keywords
- 銑刀
- 立銑刀
- milling cutter
- フライス盤